From high in the sky to desktop, remote crane technology safer and more productive
By SUSAN GREEN
Staff Writer
BNSF has North America’s largest intermodal facilities spread across our network, where we use cranes to load containers on and off trains for further movement by railroad or by truck to their final destination. Some of these are wide-span electric cranes.
In 2007, BNSF was the first U.S. rail carrier to use wide-span electric cranes that produce zero emissions on-site and significantly reduce the number of diesel-powered hostlers (container-moving trucks) needed at our intermodal facilities due to a wider range of motion. Today, we operate 26 of these cranes at our intermodal yards.
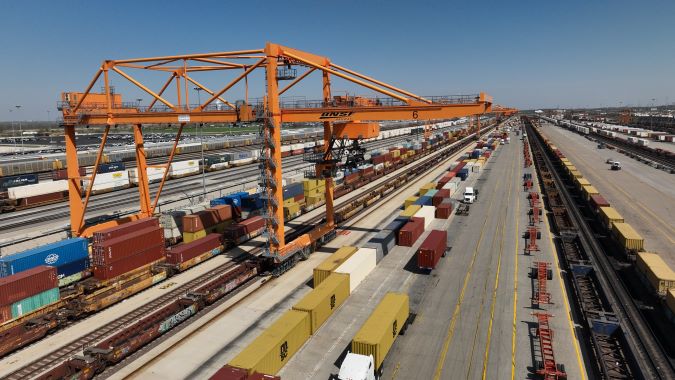
Now, thanks to a cross-departmental team’s innovation, BNSF is the first railroad in North America to develop and test a wireless solution for six remote widespan cranes at our Logistics Park Chicago (LPC) facility. The solution takes the crane operator out of the crane’s cab some 45 feet high and puts them in a nearby office space, reducing the time to get to and from the cab.
“On average, we expect to gain three hours of productivity per crane,” Jon Gabriel, vice president, Service Design, explained. “Across six cranes at Chicago, that’s 18 hours per day or the equivalent of an additional crane. This productivity gain improves the capacity of the facility by approximately 14% and provides continuous workflow for hostlers, which translates to a better experience for our customers.”
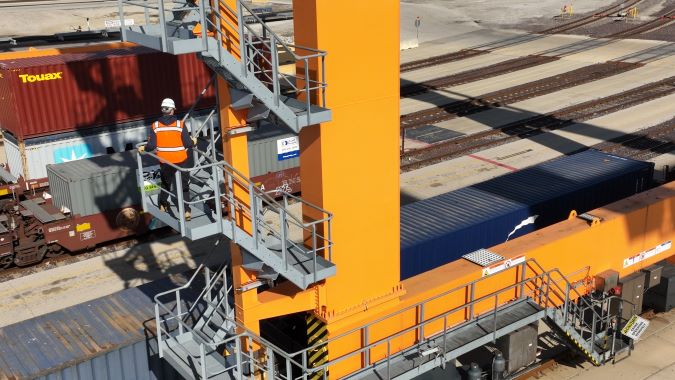
Not only are the six remote-operation cranes making us more efficient and creating more capacity they’re also making it safer for those who operate these cranes. With the cab of the crane located nearly five stories high, by having operators managing the cranes remotely from an office desk, risk is reduced – as is the time it takes to climb up and down four flights of stairs at shift change.
To transition from traditional wide-span electric cranes to the remote version requires mirroring the crane operator’s cab environment to a remotely controlled desk space. “We're using cameras and a new technology, then connecting with those crane controls not unlike a gaming console and then mimicking what they can do in the cab to the office,” Cari Elstad, manager, Technology Services, explained.
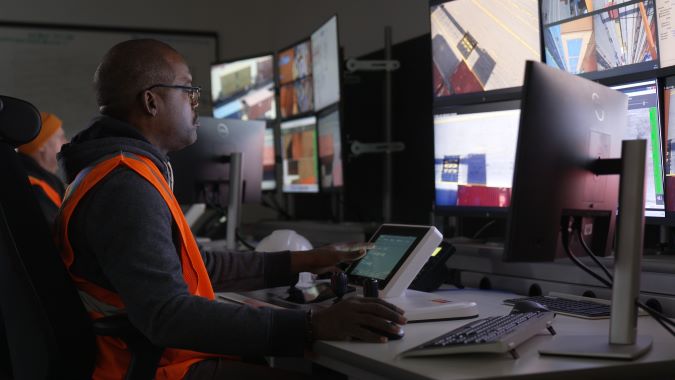
From the user’s standpoint, the transition has been positive. “Once the operators were comfortable with the setup, the majority preferred to be at the desk and were eager to sign up for certification,” Elstad added.
They also appreciate the efficiencies and safety aspects compared with the cab environment. “When you work in a crane cab, you might go up two times and down two times the four flights of stairs,” Norman Hardy, a remote-control crane operator at LPC, said. “Now, when I come to work, I can get out of my truck, walk in and get to work in as little as five minutes.”
The LPC facility is one of three that can do more than 1 million lifts a year. “We plan to keep rolling out this technology across the network. The beauty of the wireless solution is that it’s scalable,” Gabriel noted. In the coming months, we plan to start rolling the technology out next at our Memphis, Tennessee, intermodal facility and then Logistics Park Kansas City in 2024.
Innovating crane operations is just one example of how we’re adapting technology to create capacity, improve consistency and build-in safety.
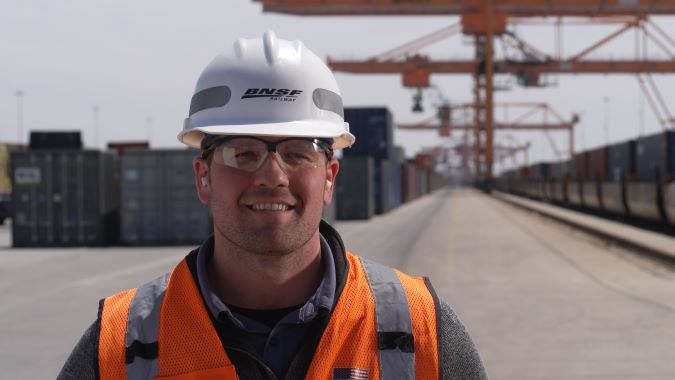
“Moving to remote operation of these cranes is positioning us well for future advancement and efficiencies to continually improve the customer experience and get that unit on a truck and the truck out of the facility as safely and efficiently as possible,” Tim Worrell, assistant superintendent, Transportation, at LPC, said.
September 2024 Update
Since this story was originally posted, we have seen the investments in this new technology really pay off, especially as intermodal volumes coming through the West Coast are beginning to ramp up, Group Vice President of Consumer Products Jon Gabriel said.
“The remote-control crane innovation at LPC, where many containers are processed as they head to and from the West Coast, has reduced the time it takes to lift containers at shift change by more than 50 percent,” Gabriel said. “This then reduces turn-times in the facility for outside drivers delivering and pulling freight, while increasing the capacity of the facility for our customers.”
And we’re continuing to see safety enhancements, thanks to the ability of crane operators to work in an office environment instead of the crane’s cab.
“By not having to climb up and down the nearly five-story-high crane cabs in extreme weather, be it heat or snow or ice, we’re reducing the risk to our people,” said Scott Hernandez, assistant vice president of Intermodal Strategy & Innovation. “We can also attract a new work force that’s accustomed to being behind a computer very similar to gaming. It’s an exciting time to work at the railroad!”