How BNSF uses gravity to sort rail cars, build trains
BNSF’s rail facilities are used to transfer the necessary goods that fuel our economy – from the grain used to make bread, to the toaster that warms the final piece of your breakfast. Our series, the Fundamentals of Facilities, will highlight some of our key facilities in that process and how they work in transferring different commodities to other modes of transportation, ensuring the delivery of goods to their final destination.
Hump day is celebrated as the midpoint of the week, when people climb over the metaphorical crest of the hill. For BNSF, hump day is every day at our eight hump yard facilities that help us sort and group freight cars destined to arrive at specific locations.
Hump yards, also known as classification yards, are generally segmented into three parts: the receiving yard, the classification bowl and the departure yard. A manifest train carrying mixed freight enters the receiving area and prepares for sorting by climbing a small artificial hill on the lead track. At the crest of the hill, a yard worker then uncouples from the train a single car or a block of cars that are intended for a specific destination track.
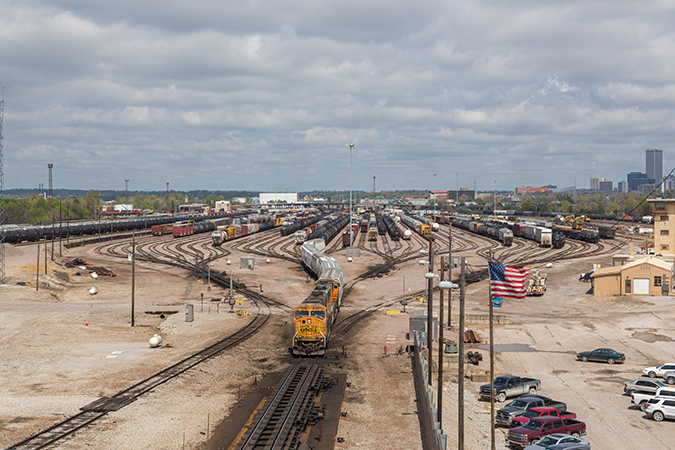
The gravity of the hill provides the necessary energy to propel the car or block of cars into the classification bowl, which features an array of switches that direct cars to different tracks that have an assigned destination. Retarders, or stationary brakes located on the tracks, safely control the speed at which the cars travel into their designated destination tracks. Cars then join other cars that have the same destination and are coupled together to build a new manifest segment of railcars.
At the departure yard, locomotives are assigned and join a congregation of railcars. Once the newly-formed train is inspected for safety, it leaves the hump yard toward its destination. There are several thousand railcar movements a day at each facility by way of hump, pull, arrival or departure.
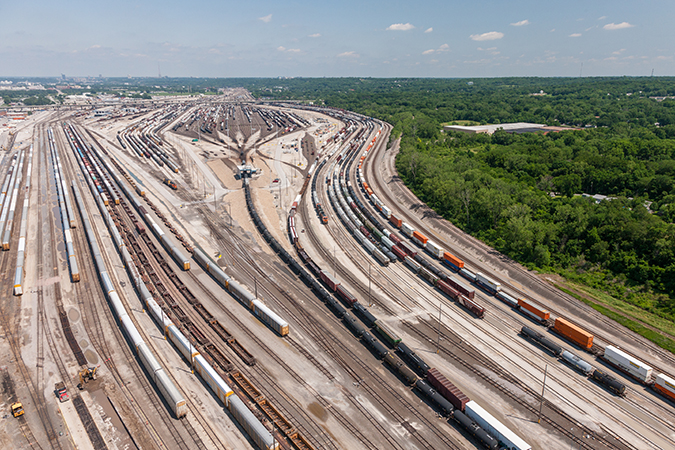
While the basics of a hump yard have been around for over a century, technology and processes have evolved to help sort and plan the movement of the ever-growing number of railcars that travel on our network. In 2018, BNSF completed a multi-year, cross-departmental project that modernized our hump yard network by implementing Terminal Process Control (TPC) technology.
“TPC is a significant enhancement of our data processing capabilities that elevates our ability to sort and reclassify railcars more efficiently at our hump yard facilities, which in turn makes work even safer for our employees by eliminating equipment touchpoints,” said Jerad Fritz, assistant vice president, Signal. “The development and implementation of the technology was completed in-house at BNSF and is a proud achievement that is shared by a team featuring members from our Engineering, Technology Services, Telecommunications and Transportation departments.”
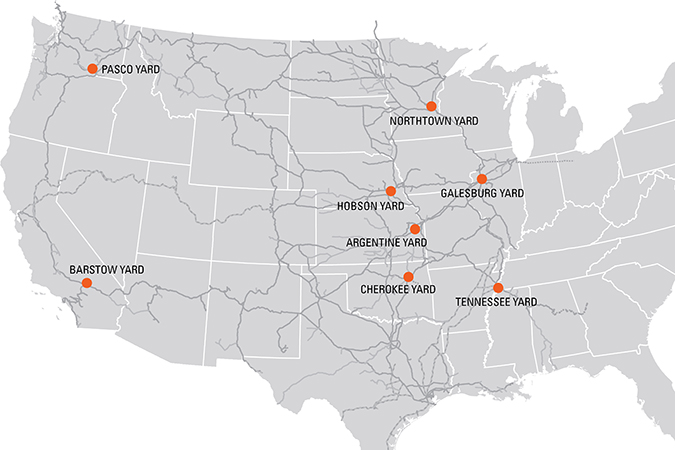
TPC has been installed at all eight BNSF hump yards: Barstow, California; Galesburg, Illinois; Kansas City, Kansas; Lincoln, Nebraska; Memphis; Tennessee; Minneapolis, Minnesota; Pasco, Washington; and Tulsa, Oklahoma. The first installation occurred at the Memphis hump yard in late 2015. Installation continued at a steady pace until TPC was fully operational across our network at the end of 2018.
TPC integrates specific hump yard details, such as the degree of each curve, number of switches and grade incline or decline percentage, to ensure accurate calculations for safely sorting each railcar. Data from each hump location is stored in a central repository and used to improve processes across our entire system. In fact, we are currently taking the next steps with the technology and refining new ways to enhance end-to-end decision-making across our network, further reducing the time it takes a railcar to get from origin to destination.
“The biggest advantage of TPC over our previous system is derived from the expertise gained across all our departments involved in the development and usage of the technology,” said Steven Philips, director, Signal. “Previously we had to rely on outside vendors for changes to our hump yard technology and equipment, but now we control our own destiny with a knowledgebase of standardized, state-of-the-art equipment and systems used throughout our network. Our TPC experts can use the data output to customize transportation solutions that more efficiently fit the needs of our customers.”
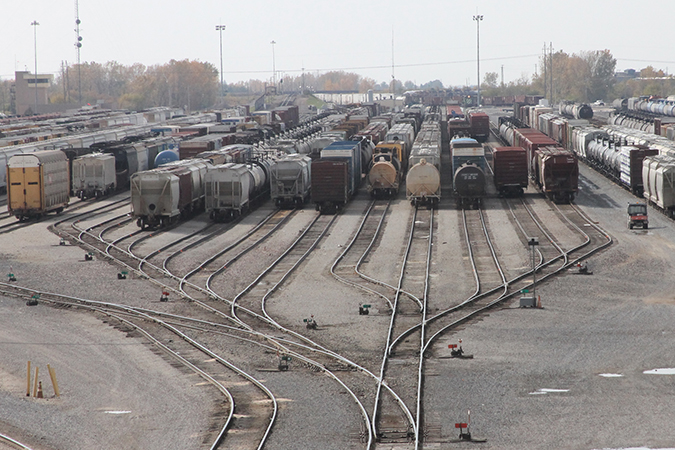
Hump yard facilities play an important role on the BNSF network, and as with all of our facilities and processes, we are constantly looking for ways to increase safety and efficiency. TPC makes this possible and gives us cause to celebrate hump day 365 days a year.
Did You Know?
In the month of April 2021, the team at the Galesburg hump yard broke four individual all-time, average-cars-per-day records for cars humped, pulled, arrived and departed. Most importantly, this monumental achievement was reached safely without injury. The new average-cars-per-day facility records now stand at 1,888 humped, 1,923 cars pulled, 1,721 cars arrived, 1,847 cars departed.