Delivering what matters: BNSF works with customers to move essential goods during pandemic
Supply chains are usually much smoother sailing in ordinary times, and most people rarely think about them. But the impact of the COVID-19 pandemic has made highly visible waves. In fact, some might call it a tsunami, leading to short-term essential goods shortages. As shoppers empty shelves of non-perishable goods and paper products, grocery stores may at times resemble a post-apocalyptic movie.
BNSF knows what people are going through, and we’re doing our part to deliver what is needed. “Team BNSF and our service partners are working tirelessly with some of the nation’s largest consumer brands and store chains to transport essential goods where they are needed most during this unprecedented time,” said BNSF Group Vice President of Consumer Products Tom Williams.
That’s because shipping goods across the nation requires a partnership between ocean carriers, trucking companies and railroads to make the magic happen. We’re proud to work with more than 200 trucking companies and asset-based intermodal service providers, including some of the nation’s largest: J.B. Hunt, Schneider, Swift and C.H. Robinson to name a few.
When a shipping container arrives at a port or intermodal terminal, it starts a journey that crosses many state borders, following rail lines and highways before coming to your local supermarket or home improvement store. Typically when a shipment arrives at a port, goods will travel inland by rail in the container they arrived in or are taken to a transload facility by truck. At the transload facility the shipment is transferred to a bigger container before its journey by rail begins.
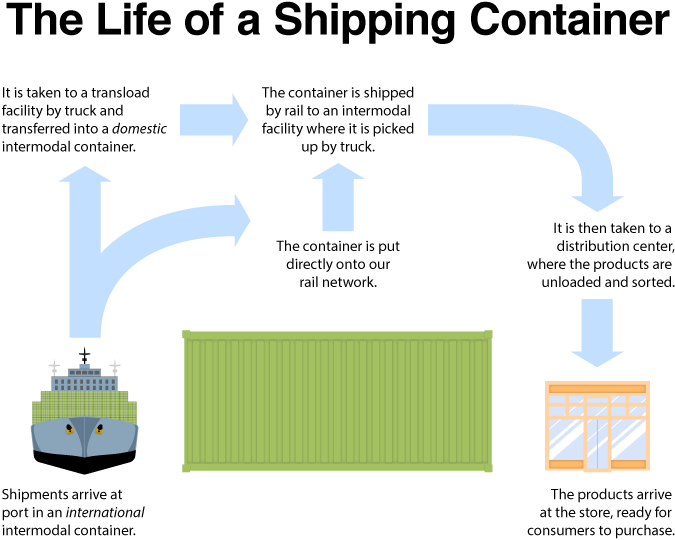
Once the container makes it onto the rails for the long haul, it will travel to one of our 25 intermodal facilities, such as our logistics park in Chicago. There it will be picked up by truck and taken for the short haul, typically less than 200 to 300 miles, to another location, usually a distribution center. There goods are unloaded and sorted before making their way to their final destination and onto store shelves.
Here are some ways our teams are working with customers and service partners to keep the U.S. supply chain moving.
Providing the Capacity to Deliver
When China was forced to put several regions on lockdown and manufacturing paused due to an increase in COVID-19 cases, it caused a delay in freight shipments to the U.S. ports on the West Coast.
As a result, not enough containers filled with goods are moving from the ports inland causing an imbalance of empty containers because there isn’t enough freight being shipped back to return the containers and start the process over again.
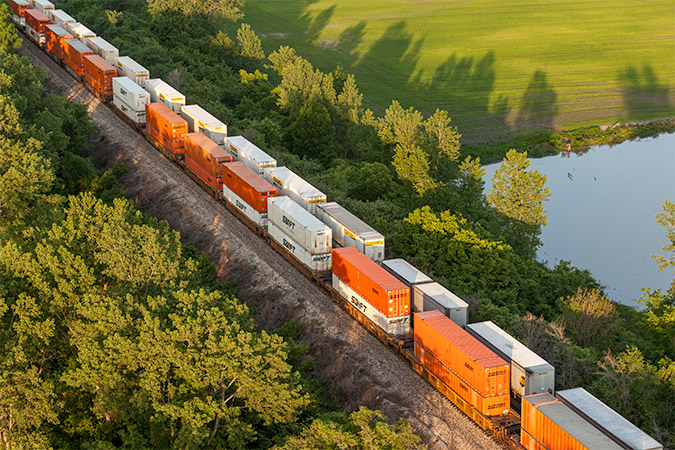
To combat this bottleneck, we’re working with our carrier partners to reposition equipment and empty containers and increase capacity to continue distributing essential goods without a delay.
Consistent Level of Service
While the logistics of where freight shipments are coming to and from have shifted due to a decrease in imports, one thing has remained constant: the level of service that we’re providing.
BNSF has the largest intermodal network in North America covering a vast geographic area. Thankfully, throughout the years we have made significant investments in our network and technology so we can provide consistent service in a time of increasing demand for much-needed shipments.
Providing this consistency allows leading retailers like Walmart and Target, which have seen a large increase in grocery and paper product demand as well as a surge in online and store pick-up orders, to continue getting the products everybody needs without fear of delay.
Additionally, Kimberly-Clark, the manufacturer of several well-known brands for things like toilet paper, diapers and personal hygiene products, saw a huge increase in demand as consumers started stockpiling these supplies. As they’ve worked to match supply with this newfound demand, we’ve adjusted our operations accordingly.
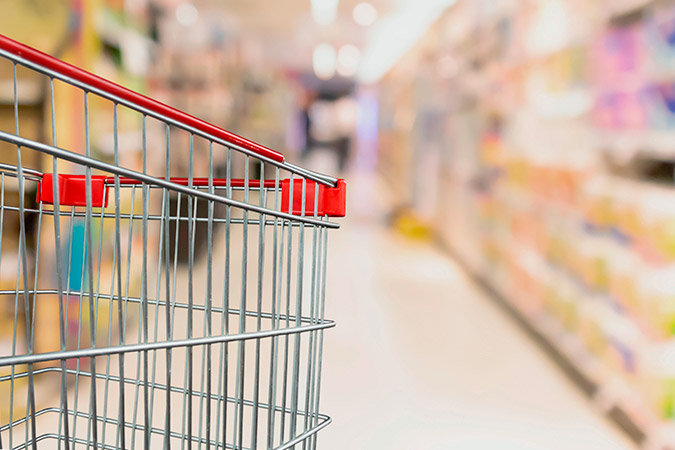
To help businesses better understand intermodal and the value it offers, BNSF has an Intermodal Solutions Team of about a dozen people strategically positioned around the U.S. and Mexico. “We are working daily with our customers to help them figure out how to best deliver the goods that communities depend on,” said Gregg Zody, general director for the team. “We’re continuing to do that during the COVID-19 pandemic while adjusting for an increased need for their goods and services.”
But it’s not just grocery stores and manufacturers that have seen a sharp increase in demand. Home improvement stores like Lowe’s have had the same experience as they work to provide essential products and services to customers, government officials and first responders in response to COVID-19. Lowe’s customers are depending on their stores for urgent needs like refrigerators and freezers, generators, hot water heaters, cleaning products and safety equipment.
Race Against Time
As shipments arrive on our network, we work with customers to prioritize delivery of essential goods and stay in constant communication with them about their needs.
Some customers are having to adjust their shipments just so they can keep their products on store shelves. Del Monte, a lead provider in shelf stable and ready-to-eat foods, is experiencing peak-level volumes that are typically seen near Christmas. However, as consumers are flocking to stores to stock up on non-perishable items, they are having to adjust their supply chain to increase the speed at which deliveries are made. They are working with our intermodal team and carrier partners to shift their shipments from boxcars to intermodal containers, so that they can reach the markets faster and provide nourishment to the public.
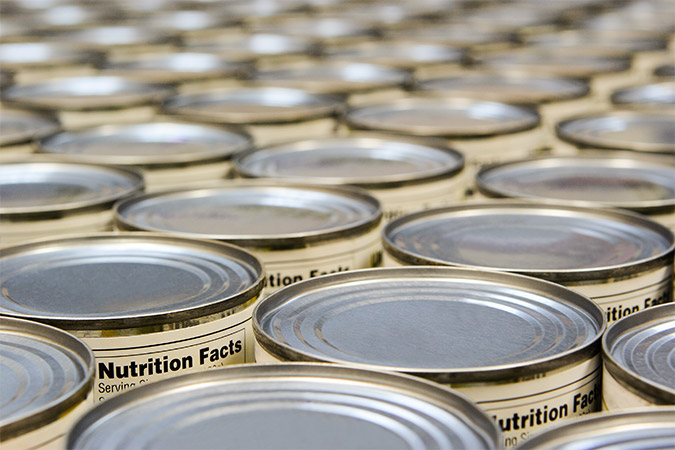
Several textile companies have also shifted their production to assist the medical community. SanMar, one of the leading suppliers in wholesale textile distribution, has changed its business focus to creating gowns and masks for medical personnel as part of a larger coalition with U.S. apparel companies. BNSF is working with SanMar to transport the medical gowns it’s producing to where they are needed most.
The flexibility of our operations and dedication to our customers mean we can provide shipping options that work for them. One shipment on our expedited intermodal train travels about 825 miles per day, while traditional intermodal shipments travel around 550 miles per day. With the increase in demand from consumers, shippers have the opportunity to expedite their shipments to reach markets faster and save critical time.
For example, Uline, a distributor of industrial and shipping products, uses our expedited intermodal service. “Uline provides essential safety, janitorial and personal protection supplies to businesses, hospitals and first responders. While the demand for these products has only increased throughout the pandemic, we've continued to work with our service partners to ensure Uline is able to keep their promises to their customers,” said Angelo Ventrone, Vice President of Logistics, Uline, Inc.
It is this teamwork mentality that enables BNSF, our carrier partners and stores to keep restocking the shelves daily. “Our relationships with our customers are extremely important,” Zody said. “It becomes increasingly clear how much it matters when there’s a crisis like this and we’re working together to serve the public.”