Driving success: BNSF steps on the gas to help automakers meet surging demand
By STEPHEN MANNING
Staff Writer
We’re in the middle of a unique moment in the history of the automotive supply chain, and rising to the occasion to meet the needs of manufacturers, dealers and consumers is the challenge facing all the interconnected parts of that supply chain.
BNSF’s Tom Williams, group vice president Consumer Products, explained what has happened. “The pandemic caused a significant slowdown in production of various parts, including semiconductor chips, which led to a steep drop in production of vehicles. Dealer inventories are starting to recover now, but they’re still much lower than their historic highs. Meanwhile, with the pandemic behind us, there’s a lot of pent-up demand for vehicles, especially in the United States.”
Manufacturers are working full tilt to meet that demand, and the vehicles they’re producing need to get to dealers. Railroads, a critical part of the automotive supply chain, have gone from watching the need for automotive transport plunge to striving to meet rising demand. Automotive customers want to move more vehicles than railroads are currently moving, and they want those vehicles delivered more quickly than railroads are delivering them.
“We know that speeding up industry wide car velocity is the key to meeting near-term higher demand for vehicle shipments, and BNSF is taking strides to do our part to help accelerate velocity,” Michael Wade, assistant vice president of Consumer Products Marketing, said.
Because the automotive supply chain is an interconnected network consisting of manufacturers, shipping lines, railroads, trucking companies and others, railroads aren’t operating in isolation. What happens on one railroad has an impact on the others and on the supply chain as a whole.
For example, most auto-rack cars are part of a pool shared by railroads and operated by TTX Company. The faster these cars are able to get across one railroad, interchanged to the next and unloaded, the sooner they can be put back into circulation to pick up more.
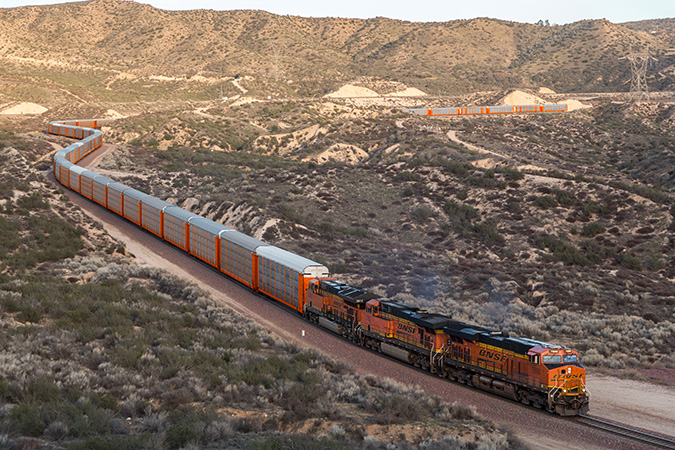
BNSF values the business of its automotive customers. We have long worked to bring innovation to our automotive service. Along with The Greenbrier Company and Honda Motor Company, BNSF pioneered the development of tri-level Auto-Max rail cars with an enhanced capacity of 22 vehicles, compared to up to 10 vehicles for a traditional bi-level auto-rack car and up to 15 for a standard tri-level. We have solutions in place to maximize the benefits of these cars, which we operate outside the TTX pool, to improve fluidity.
Our focused efforts to increase velocity in our auto network are paying off. We’ve seen a 14 percent improvement in automotive velocity this quarter while handling record volumes – and our momentum continues to build.
We have added a dedicated operational design team solely focus on improving automotive velocity and our customer experience. To highlight a few of the recent actions we’ve taken to do just that:
- We’ve restored our dedicated automotive network. When volumes declined, we intentionally moved vehicle shipments to our carload network, which means autorack cars traveled on mixed-freight trains with other commodities. Now that volumes are rising, we are bringing back automotive unit trains, or trains that carry only one type of freight.
- As BNSF improves speed and consistency to market, the risk of railcars queuing up at their destinations awaiting space to unload is a watchpoint. BNSF has recently launched new pipeline management tools, which provide manufacturers and truckers the visibility needed to improve the fluidity of destination facilities. This has the benefit of reducing dwell on loaded railcars waiting for parking space to be unloaded.
- We’ve identified creative ways to deploy our Auto-Max fleet in traditional bi-level auto-rack car lanes, reducing reliance on bi-levels and returning more bi-levels to origin points awaiting much needed car supply.
- We’ve purchased 740 bi-level autorack cars to supplement our fleet in the TTX pool.
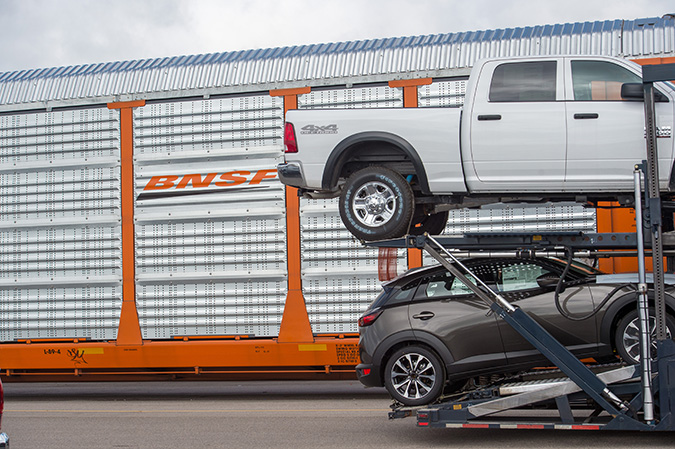
BNSF is committed to addressing the equipment and velocity factors we can control. As part of a collective rail network, we believe what we’re doing to improve our own velocity will contribute to the betterment of the industry.
“Manufacturing is back, and manufacturers are not going to stop making vehicles,” Williams said. “We have a collective supply chain. No matter who we are in that chain, whether we're a railroad, manufacturer or other, we all have a role to play in getting those vehicles to consumers. There has been a lot of change in the industry in the last three years, with more alternatives for transport. Shippers will do what they have to do to get to market.”
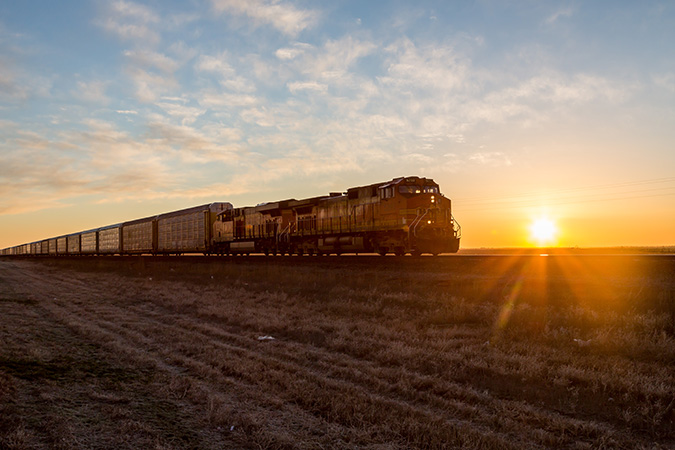
A key component of the solution, Williams said, is collaboration with all parts of the automotive supply chain. He cited the recent BNSF Haulaway Summit, the first to be held in person in three years, as an opportunity for players in the supply chain to work toward a cooperative plan of attack for ensuring that vehicles that arrive to their final BNSF destination station are picked up and moved to automotive dealerships to make space for more trains to be unloaded. BNSF was one of the founding pioneers in the industry event, which has helped players in the supply chain hand off vehicles more efficiently.
“We need the entire railroad industry working together to solve this,” Williams said. “When the industry succeeds at increasing the collective network’s velocity, not only will we help manufacturers and consumers, but we'll help ourselves by moving more volume.”