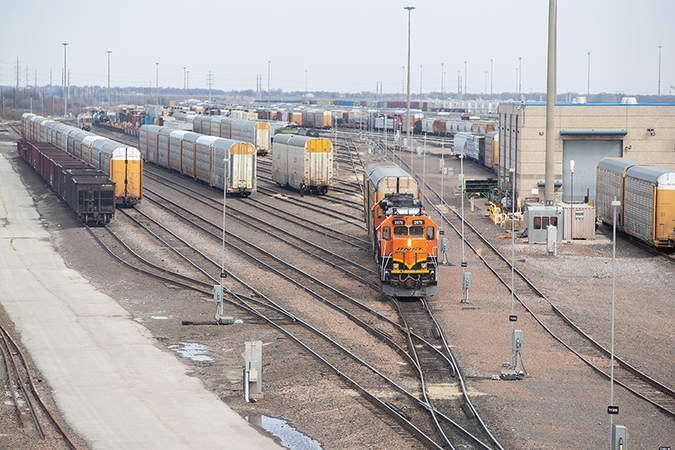
Getting into the 'rithm: New switching technology boosts safety, efficiency
Switching railcars is nothing new for railroaders. It's a process that generations of them have performed for more than a century, and it’s at the core of how we’ve served multiple origins delivering to thousands of destinations for our customers.
Consider this: if we had a four-track yard that held 10 rail cars, and these 10 cars needed to be switched into three separate trains – there would be more than 5 million combinations of how this could be done—and there is one optimal way.
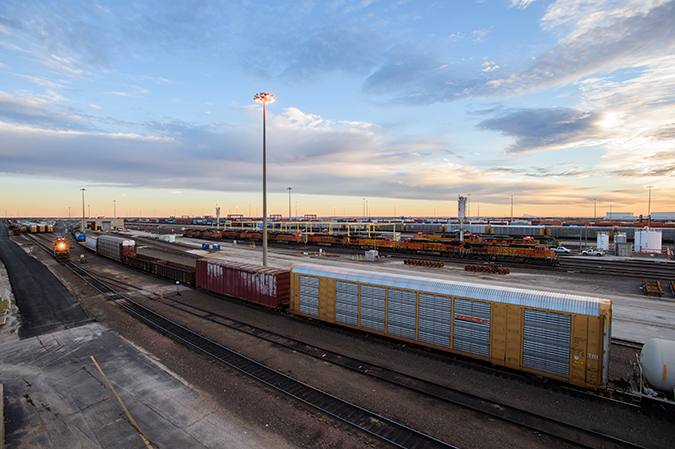
Historically, we’ve relied solely on the experience of the person marking the switch list to manually think through the millions of combinations to best switch cars. However, a new and innovative concept pioneered by the BNSF employees who perform this work will change the game on switching. Using artificial intelligence and machine learning techniques, we recently developed an automated way to create an algorithmically planned and optimized switch list for merchandise railcars needing to be switched.
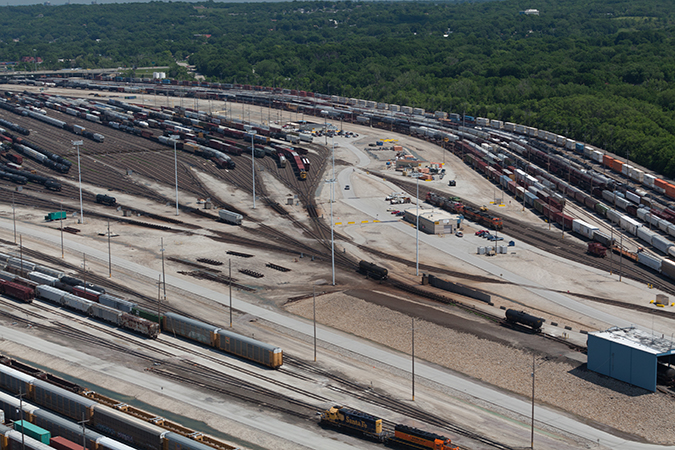
This helps our terminal teams spend less time reviewing and combing through the millions of ways to best switch the cars, giving us more time to perform the work switching our customers’ freight. By enhancing human decision-making and reducing variability from the switching process, this approach helps improve our service consistency and enables us to say “yes” to more freight from our customers. Reducing the number of switch moves also makes the environment safer for our employees. We’re excited to see the results this change brings us.
Big thanks to our BNSF teams, from our world-class employees who pull the freight and plan the work to our industry-leading data scientists who worked with them to think through this game-changing technology.