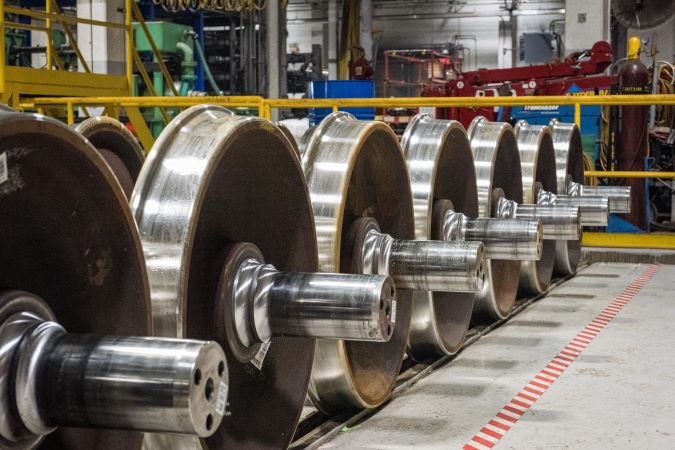
‘Wheel’ you believe it? How BNSF monitors wheel health across the network
By PAIGE ROMANOWSKI
Staff Writer
The average railcar wheel will travel around 500,000 miles in its lifetime, or 15 trips across the entirety of our 32,500-mile network. BNSF’s mechanical team is responsible for ensuring each wheel is in excellent operating condition. With more than 200,000 railcars, and more than one and a half million wheels in motion across our network at any time, our condition-based maintenance team uses a variety of detectors to stay on top of each wheel’s condition.
“Our coverage is carefully planned and purposefully laid out,” said Hark Braren, director of mechanical engineering in BNSF’s mechanical department. “Wheel health and performance is monitored in a variety of ways, from its impact on our rails, to its temperature, how it sounds and even how it looks. To accomplish this, BNSF’s network is strategically equipped with technologies to monitor each aspect of wheel health with a layered safety approach.”
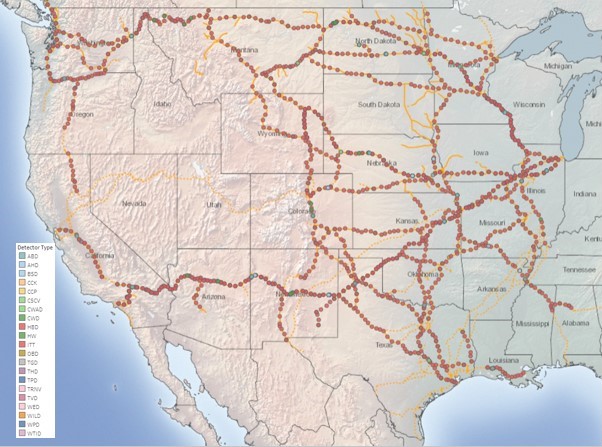
Here are some of the tools we use to ensure our wheels are in tip-top condition:
Wheel Tread Inspection Detector
One of the most prominent systems is wheel tread inspection detectors (WTID). Designed to capture the entire tread surface and plate of a wheel set, this machine vision system can find defects and send alarms to the detector desk – which helps determine the severity of the defect and appropriate handling for each wheel’s inspection.
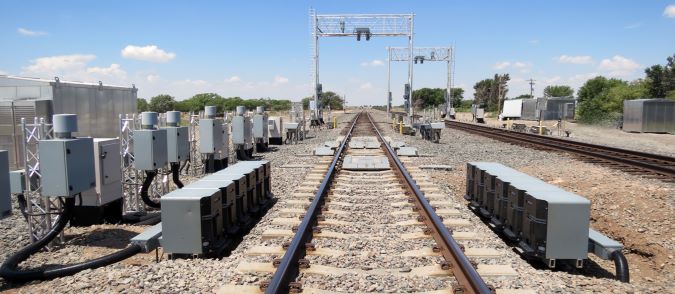
“We pride ourselves in terms of our industry-leading development,” said Braren. “BNSF drove the development of WTID, which uses high resolution camera technology to automatically inspect the wheel tread, flange and plate surface areas around the entire circumference of the wheel. The system is now being used in France, Australia and Canada.”
WTID images are processed with a variety of machine vision models, created in-house by our image and video analytics team with the help of artificial intelligence, to analyze the wheel surface conditions. It uses images taken from multiple angles of the wheel surface to find any visible defects. Our technology continuously evolves, enhancing its ability to not only detect current wheel irregularities but also predict potential issues hundreds of miles down the track.
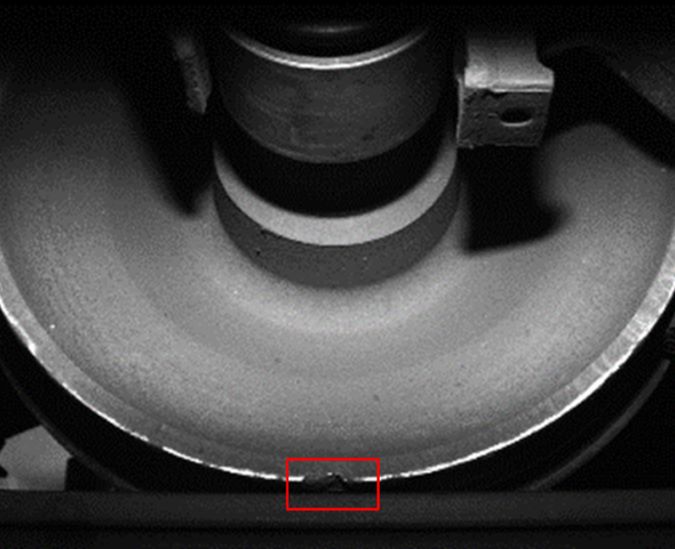
“The WTID system provides us with a detailed inspection of each wheel, so we know its condition before it reaches destination,” said Ryan Cline, senior manager of equipment operations at BNSF. “It’s so reassuring to know that WTID is helping us identify defects and mitigate their associated risk.”
Brake Health Effectiveness Detectors
The surface appearance isn’t the only factor determining a wheel’s condition. Temperature is another. Using thermal detectors, our brake health effectiveness (BHE) technology helps identify brake system related issues.
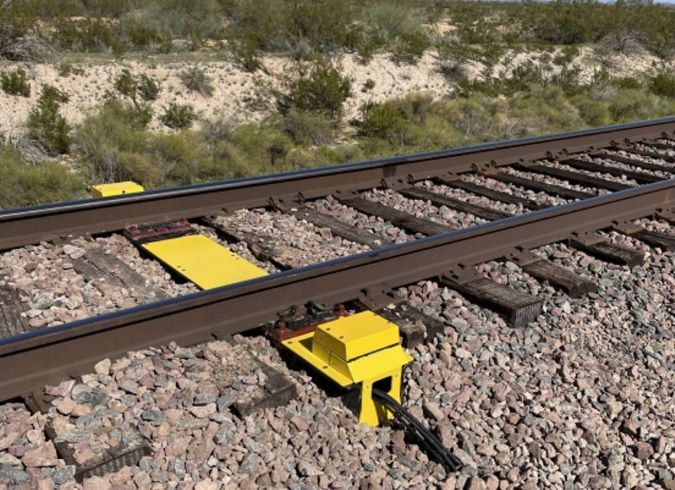
To gauge a wheel’s temperature, a train must run past the detector twice: first without the brakes applied and once again with the brakes applied. If a wheel registers as hot while the brakes are not applied, the crew is notified of a potential sticking brake.
While hot wheels are occasionally found, BHE’s primary function is finding cold wheels caused by a brake system not working as intended (for example, if the brakes are applied and no heat is detected by the system). The brake system’s proper functioning is key to a wheel’s health and longevity.
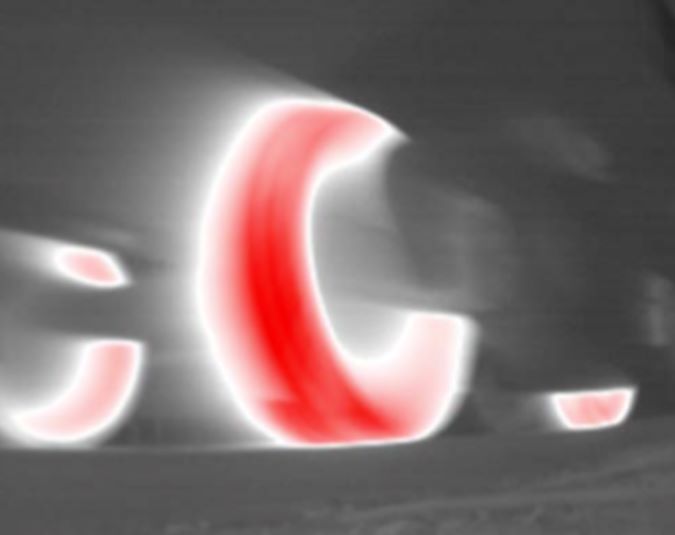
Wheel Impact Load Detector
Wheel impact load detectors (WILD) consist of sensors attached to the rail that monitor the tread surface condition of a wheel as it impacts the railhead. The primary function of a WILD is to find high impact wheels, typically caused by a flat spot or other wheel defect, which can be damaging to both equipment and track structure. Also, with thousands of pounds of force running across the rails, wheel weight measurements are used to spot overload and imbalance conditions, which can lead to extra wear and tear.
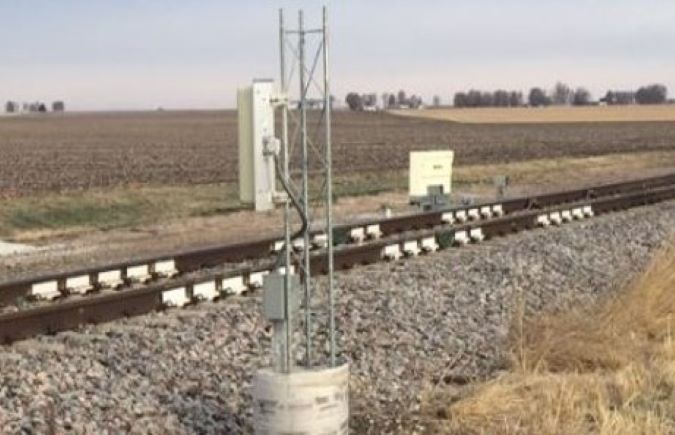
In years past, if the detectors discovered a defect, the train’s dispatcher would be notified. The dispatcher would then call the train crew and give instructions on how and when to set the car out for repair. Today, dispatch is still immediately notified, but Positive Train Control (PTC) technology simultaneously sends alerts directly to the locomotive engineer for the most severe alarms.
When a wheel needs to be replaced, we don’t replace one wheel, we replace the affected wheel set. Like all things on the railroad, safety and efficiency are key.
“The alarmed wheel set is then sent to our Havelock wheel shop for repair or to be recycled,” explained Cline. “The time to make repairs varies by car type – most conventional four-axle cars take 30-45 minutes, but on a more complex car, like an intermodal car, it can take a couple hours.”
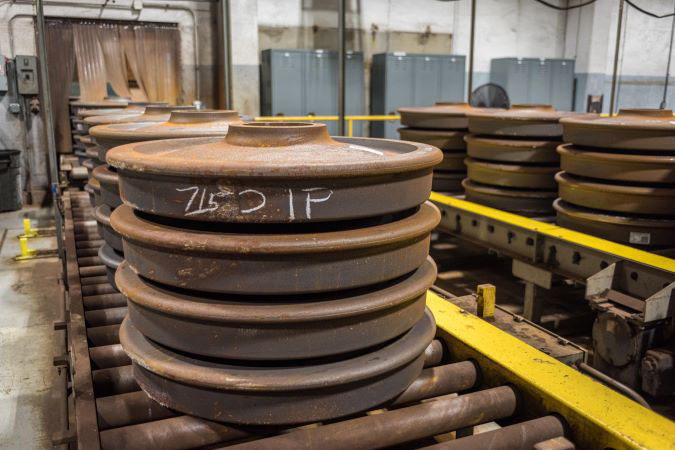
Keeping our fleet in optimal condition isn’t just important for the longevity of our equipment, it also helps keep the supply chain rolling smoothly and safely.
Thank you to our engineering and mechanical teams working hard every day to create the safest railroad.